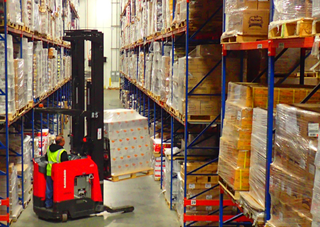
As the mid-point between your manufacturing facility and your customers, your warehouse is the heart of your supply chain. Without a proper warehouse setup, your supply chain will not flow smoothly, resulting in possible shipment delays or even worse, your customers receiving product that could be expired! One of the most important aspects of your warehouse setup is choosing the proper inventory rotation technique based on the characteristics of your products. Unfortunately, most discussions about inventory rotation methods revolve around confusing acronyms that are often not fully understood. Here’s a simplified breakdown of the most common inventory rotation methods:
FEFO – First Expiry, First Out or Oldest Production Date – This inventory rotation technique ensures that the oldest product leaves the warehouse first because inventory is being rotated by the expiration date or oldest production lot code. FEFO rotation also ensures that any returned product is received in properly, based on the expiration date and put back into a proper rotation sequence.
*Our tip – for ease of translation, your lot code and expiry date should be formatted as like this: “Jan/01/2018”. With this format, the month, day and year should never be misinterpreted for one another, avoiding the possibility for a serious mix-up.
FIFO – First In, First Out. The simplest rotation method and the method that many companies choose even though it may not be ideal for their product. The issue with FIFO, especially with perishables, is that returns are not properly processed. Even though your warehouse is likely receiving most of your product in the order it’s produced, any returns will be received back into inventory based on the date of the return, not remaining product life.
LIFO – Last In, First Out – This rotation method ensures the newest production run is shipped out first. This is ideal if your product loses value quickly and doesn’t expire.
Batch Tracking – Can be utilized if your product is received in sequential batches. This method allows you to group up multiple batches to be shipped out together.
As a manufacturer or importer, you should be able to trust your warehouse partner to rotate your product properly. Whether it’s coaching a startup importer or partnering with an established brand, we at Tyler Distribution Centers work with our customers to understand their needs and discuss the right way to rotate product. If you’ve experienced inventory loss because of poor rotation, have customers that require varying amounts of shelf life and you value properly rotated inventory, give us a call.