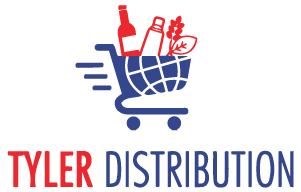
The Last Mile Problem
What is last mile delivery? In a product’s journey from warehouse shelf, to the back of a delivery truck, to a customer’s doorstep – the “last or final mile” of delivery is the last step in the process. This is the point when the package finally arrives at the buyer’s door. This step is both […]
Read More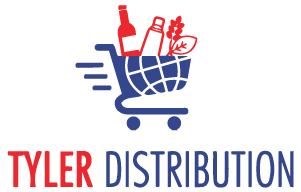
Floor (Bulk) Storage Vs. Rack Storage
If you’re asking yourself whether you should use Bulk Storage or Rack Storage, you’ve come to the right place! Let’s start by looking at how the two compare. Floor (Bulk) Storage The most inexpensive storage method allowing for high storage density. These storage areas will be in a designated area of the warehouse organized in […]
Read More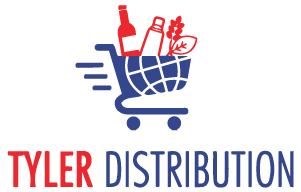
Labeling – What are some best practices for labeling your products?
In the world of supply chain, data and accuracy leads to success. The easier it is to obtain accurate data, the smoother operations will flow. Being able to quickly identify products is vital in every touch point in your supply chain. What are some best practices for labeling your products? 1. Include an item number […]
Read More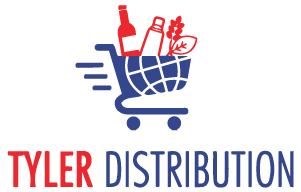
Case Picking Vs. Pallet Picking
How do the two stack up? Case Picking A product is picked in full case/carton quantities from a particular storage medium – such as a pallet position. As the picker travels the aisles selecting product, orders are grouped by various factors like size and weight. Those items are then placed on a pallet for shipment. […]
Read More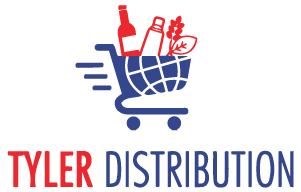
Inbound & Outbound Appointment Scheduling – Key Factors That Impact Cost
What should you pay attention to when scheduling inbound or outbound appointments with your warehousing partner? Schedules Fill up FAST Most providers will ask that they be given certain lead times between the request and the appointment date. Each provider will have different scheduling requirements and availability based on their individual operation, but one thing […]
Read More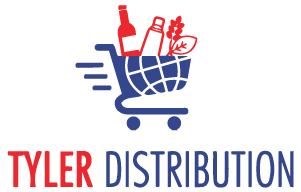
Floor Stacked Containers – What are some factors that could impact unloading costs?
This method is popular among food importers. Profit margins are often thin when maximizing every inch of space for shipping is vital. How effectively containers were loaded can have a significant impact on the cost to unload it. 1. Quantity of SKU’s and LOT’s Keep it Simple. Ideally, each container should be loaded with 1 […]
Read More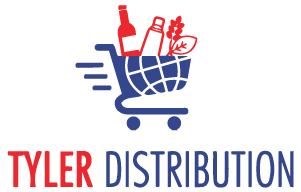
Inventory Turnover – Why is it so important? How can you determine your inventory turnover rate?
Inventory turnover is defined as the frequency in which inventory is cycled through a warehouse within a given period of time. It is one of the best metrics to determine how well inventory is being managed. If you are working with a 3PL warehouse, your pricing will be heavily based on your annual inventory turnover […]
Read More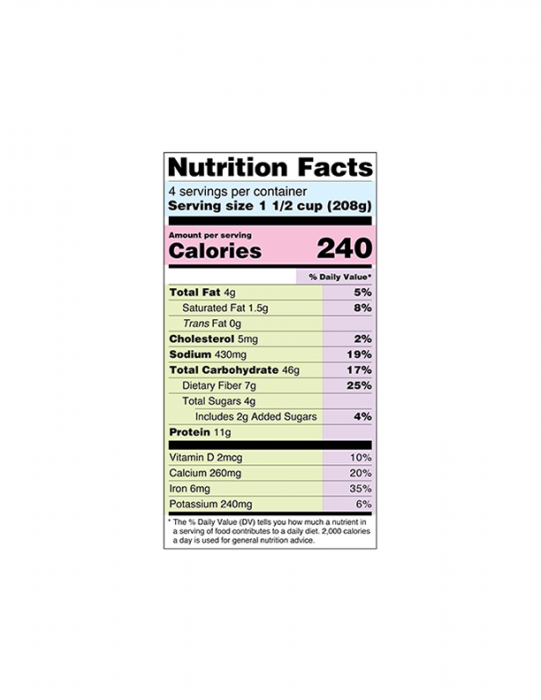
Are Your Nutrition Facts Labels In Compliance with the New Format?
Consumers are confused. In an era of information overload, consumers don’t know what’s accurate or who to trust. In a world where social media influencers and their diet trends are trusted more than medical professionals, it’s essential for you to be able to convey your products’ nutritional information clearly and simply. Because consumers are presented […]
Read More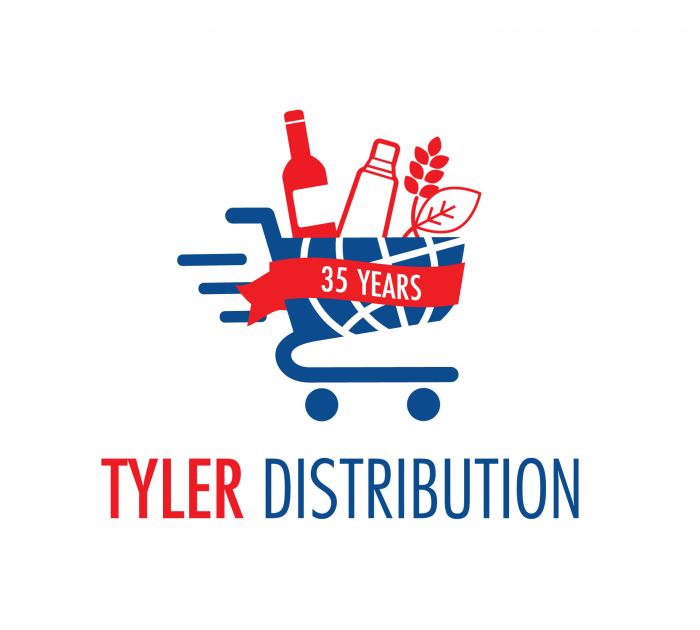
Tyler Distribution Turns 35 – This Is What We’ve Learned About Warehousing and Distribution
October 1st, 2019 – Distinguished public warehousing provider Tyler Distribution turns 35. Founded in 1984 as an expansion into the growing Central New Jersey warehousing market, today Tyler Distribution operates close to 1,000,000 square feet of public warehousing space. Originally focused on storing specialty food products for importers and domestic manufacturers, Tyler Distribution has since […]
Read More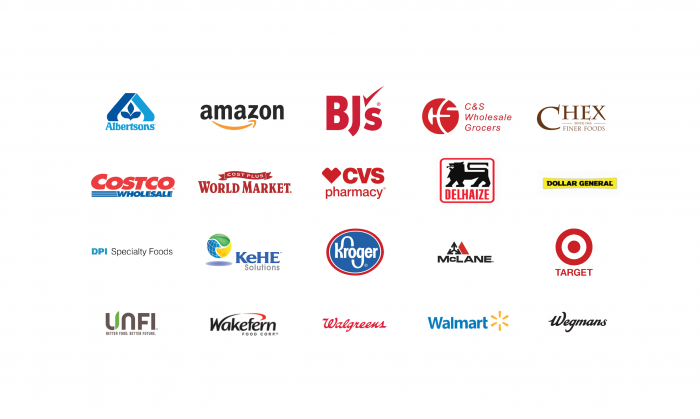
How The Right Warehousing Provider Can Help You Grow Your Retailer Relationships
Success is a puzzle. When the next big thing fails, everyone is left questioning what went wrong? Was there too much competition? Was there a lack of quality? Was there enough planning? While there isn’t a definite formula to success (if there was, everyone would use it), experts always seem to pin-point one common denominator […]
Read More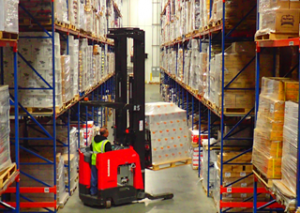
When Does it Make Sense to Utilize a Public Warehouse?
There’s a reason that public warehouses exists: the requirements to start and operate your own warehousing operation are intimidating and prohibitive. Not only do you need to find a building and staff, but you also need to learn how to manage the daily operations and have a lot of capital to invest in getting started. […]
Read More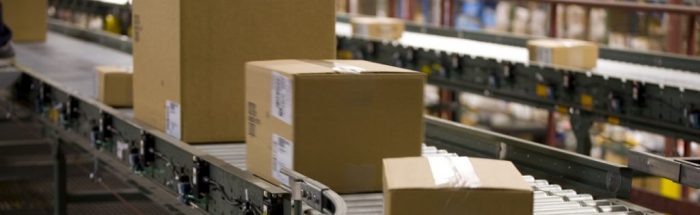
Are Your Orders in Compliance with Retailer Shipping Labeling Requirements?
When it comes to business buzzwords, optimization is often at the top of the list. With numerous methods out there, such as Lean and Six Sigma, there are various steps that a company can take to gain efficiencies. One of the major areas where companies are focusing their optimization efforts is the supply chain, with […]
Read More